Introduction
When it comes to electrical projects, whether you’re installing new wiring in your home or updating an existing system, one critical component often overlooked is the electrical wire connectors. At One & Only Electrical Service in San Diego, we understand that the right wire connectors can make a significant difference in the success of your project. This guide explores the importance of choosing the right electrical wire connectors and how they can help you avoid costly mistakes.
The Importance of Electrical Wire Connectors
Electrical wire connectors are essential for ensuring safe and reliable electrical connections. They connect various electrical wires together, facilitating the flow of electricity. A poor choice in connectors can lead to issues such as overheating, short circuits, and ultimately, potential fire hazards.
Common Mistakes to Avoid
- Using the Wrong Type of Connector
- Each type of connector is designed for specific applications. Using the wrong one can result in weak connections that fail over time.
- Overloading Connectors
- Connectors have a rated capacity. Exceeding this capacity can lead to overheating and failure.
- Improper Installation
- Incorrectly installed connectors can compromise the integrity of the connection, leading to electrical problems.
- Neglecting Insulation
- Failing to use insulated connectors in high-risk areas can lead to accidental contact with live wires.
- Using Low-Quality Products
- Cheap connectors may save money initially but can cost more in the long run due to failures and the need for repairs.
Choosing the Right Electrical Wire Connectors
1. Twist-On Wire Connectors
Twist-on wire connectors, commonly known as wire nuts, are perhaps the most versatile and widely used connectors in residential wiring. They are suitable for connecting multiple wires and are easy to use.
Benefits:
- Simple Installation: Twist-on connectors require minimal tools and skills.
- Cost-Effective: They are available in bulk at affordable prices.
- Widely Compatible: Suitable for various wire gauges and applications.
Applications:
- Ideal for connecting wires in junction boxes and lighting fixtures.
2. Crimp Connectors
Crimp connectors are metal connectors that secure wires by crimping them together. They offer a strong, reliable connection and are often used in applications requiring durability.
Benefits:
- High Reliability: Perfect for automotive or industrial settings where vibration is a concern.
- Quick Installation: With the right crimping tool, installation is fast and efficient.
Applications:
- Commonly used in low-voltage wiring and automotive applications.
3. Solder Connectors
Solder connectors create a solid connection by melting solder to join wires together. This method is often used in more permanent electrical installations.
Benefits:
- Durability: Provides a long-lasting connection that can withstand significant stress.
- Excellent Conductivity: Minimizes resistance, enhancing the efficiency of electrical systems.
Applications:
- Ideal for home automation systems or electrical vehicle charging stations where reliable connections are crucial.
4. Insulated Terminal Connectors
Insulated terminal connectors feature a plastic insulation sleeve, offering protection against accidental contact with live wires.
Benefits:
- Increased Safety: Reduces the risk of short circuits and electrical shocks.
- Color-Coded Options: Easy identification of the appropriate connector for different wire sizes.
Applications:
- Commonly used in electrical outlet installations and circuit breaker replacements.
5. Push-In Wire Connectors
Push-in wire connectors allow for quick and straightforward wire connections. Users simply push the stripped wire into the connector, making them highly user-friendly.
Benefits:
- Rapid Installation: Perfect for quick jobs or when working in tight spaces.
- Compact Design: Suitable for applications where space is limited.
Applications:
- Ideal for ceiling fan installations and various home wiring projects.
Best Practices for Using Electrical Wire Connectors
1. Match the Connector to the Application
Always ensure that the connector you choose is appropriate for the specific wires and application you are working with. Review the manufacturer’s specifications and guidelines.
2. Avoid Overloading
Check the connector’s rated capacity and ensure it matches the load of the wires being connected. Overloading connectors can lead to overheating and potential hazards.
3. Ensure Proper Installation
Follow best practices for installation, including stripping wires to the correct length and ensuring a secure fit within the connector.
4. Regular Inspections
Regularly inspect electrical connections, especially in high-use areas. Look for signs of wear or damage, and replace connectors as necessary to maintain safety.
5. Consult a Professional
If you’re unsure about your choices, don’t hesitate to consult a licensed electrician. At One & Only Electrical Service, our team is ready to assist with any electrical wiring needs you may have.
Frequently Asked Questions (FAQ)
Q1: What are the most common types of electrical wire connectors?
A1: The most common types include twist-on wire connectors, crimp connectors, solder connectors, insulated terminal connectors, and push-in wire connectors.
Q2: How do I know which connector to use?
A2: Choose a connector based on the wire gauge, type of connection needed, and the specific application. Consult manufacturer specifications for compatibility.
Q3: Can I use any connector for high-voltage applications?
A3: No, high-voltage applications require connectors specifically rated for that purpose. Always check the specifications to ensure safety.
Q4: How often should I inspect my electrical connectors?
A4: It’s a good practice to inspect electrical connectors at least once a year or more frequently in high-use areas.
Q5: What should I do if I encounter damaged connectors?
A5: If you find damaged connectors, replace them immediately to prevent potential hazards. If you’re unsure how to proceed, consult a licensed electrician.
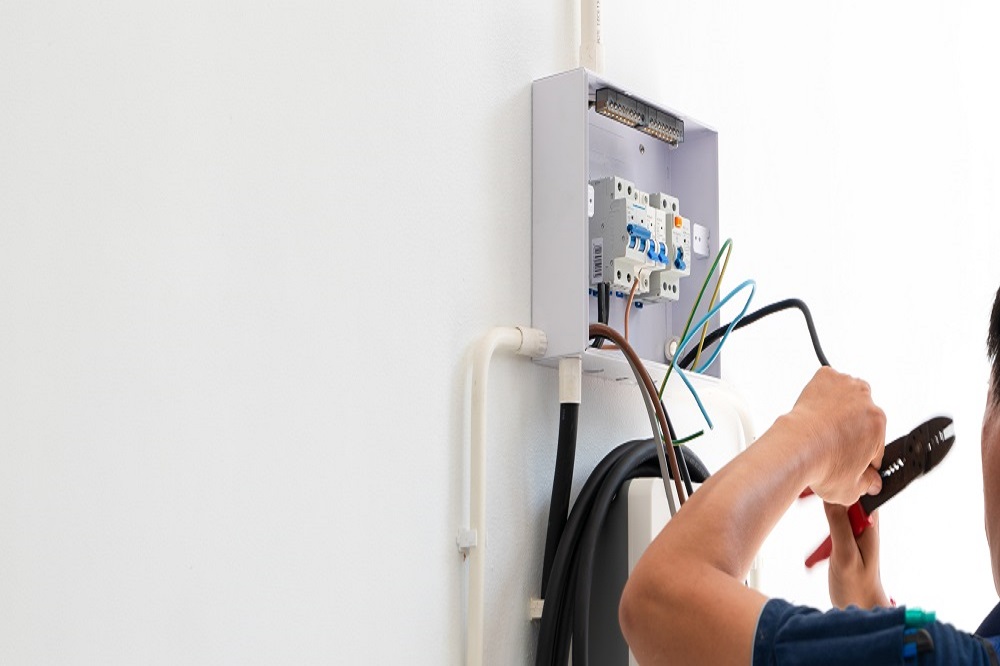