Wire connectors play a crucial role in ensuring electrical safety by providing secure and reliable connections between electrical wires. Proper use of wire connectors prevents electrical hazards such as short circuits, fires, and electric shocks. This guide outlines the various types of wire connectors and their appropriate usage to enhance electrical safety.
Importance of Wire Connectors in Electrical Safety
- Secure Connections: Wire connectors ensure that wires are firmly joined, reducing the risk of loose connections that can lead to arcing and overheating.
- Insulation: They provide insulation at the junction point, preventing accidental contact with live wires.
- Ease of Use: They simplify the process of connecting wires, making it accessible even for non-professionals.
- Durability: Quality wire connectors are designed to withstand environmental factors such as moisture and heat, ensuring long-term reliability.
Types of Wire Connectors
- Twist-On Wire Connectors
- Usage: Commonly used in residential wiring for connecting two or more wires.
- Advantages: Easy to use, widely available, and suitable for a range of wire sizes.
- Safety Tip: Ensure the connector is properly sized for the wires being joined.
- Push-In Wire Connectors
- Usage: Suitable for connecting solid wires in lighting fixtures and electrical outlets.
- Advantages: Quick installation, good for confined spaces, and reduces the risk of loose connections.
- Safety Tip: Only use with solid wires unless specified by the manufacturer.
- Screw-On Terminal Connectors
- Usage: Common in industrial applications and electrical panels.
- Advantages: Provides a very secure connection and is ideal for high-current applications.
- Safety Tip: Ensure screws are tightened adequately to prevent loosening over time.
- Crimp Connectors
- Usage: Used in automotive and appliance wiring.
- Advantages: Provides a permanent connection that resists vibration and mechanical strain.
- Safety Tip: Use a proper crimping tool to ensure a secure and reliable connection.
- Butt Connectors
- Usage: Used to connect two wires end-to-end.
- Advantages: Ideal for repairs and extending wiring.
- Safety Tip: Ensure proper insulation and use heat shrink tubing for added protection.
- Wire Nuts
- Usage: Versatile and used in various wiring applications.
- Advantages: Inexpensive, easy to install, and reusable.
- Safety Tip: Choose the correct size for the wire gauge and number of wires.
- IDC (Insulation Displacement Connectors)
- Usage: Common in telecommunications and networking.
- Advantages: Allows quick connections without stripping the wire insulation.
- Safety Tip: Ensure the connector is designed for the specific wire type and size.
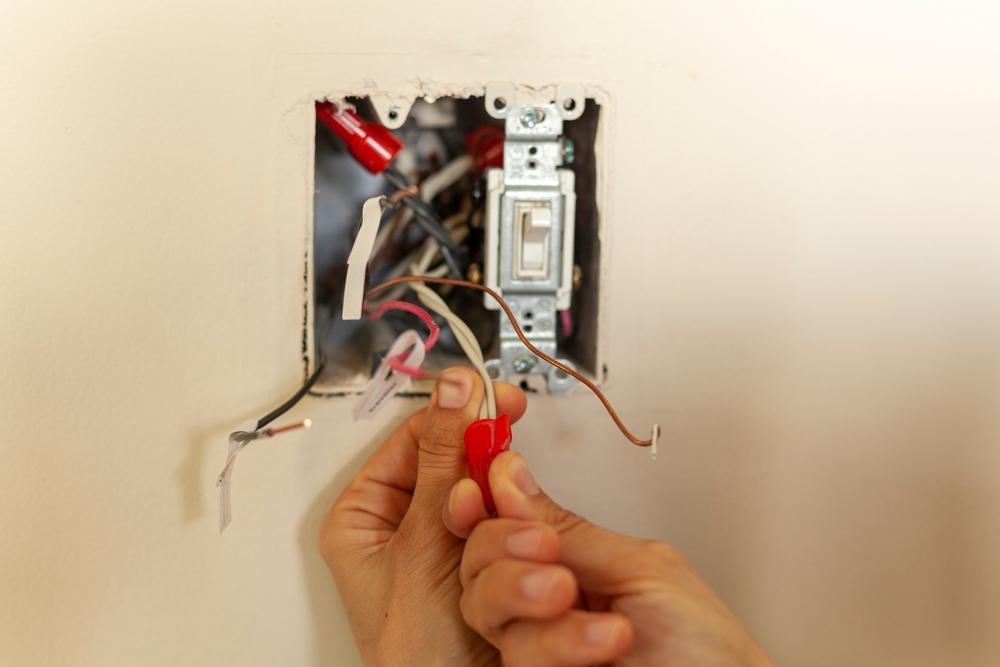
Best Practices for Using Wire Connectors
- Proper Sizing: Always use connectors that are appropriately sized for the wires being connected.
- Inspection: Regularly inspect wire connections for signs of wear, corrosion, or overheating.
- Quality Products: Use high-quality connectors that meet relevant safety standards.
- Follow Instructions: Adhere to manufacturer guidelines for installation and usage.
- Professional Assistance: For complex or high-voltage wiring, seek help from a qualified electrician.
Advanced Wire Connector Types
- Lever-Nut Connectors
- Usage: Versatile and suitable for both solid and stranded wires.
- Advantages: Easy to use, reusable, and allows for quick disconnection.
- Safety Tip: Ensure the lever is fully engaged to secure the wires.
- T-Tap Connectors
- Usage: Allows tapping into an existing wire without cutting it.
- Advantages: Simple installation, ideal for automotive and industrial applications.
- Safety Tip: Use in low-vibration environments to maintain connection integrity.
- Wire Ferrules
- Usage: Used to terminate stranded wires, providing a solid connection point for screw terminals.
- Advantages: Prevents fraying of stranded wire, ensuring a stable connection.
- Safety Tip: Use a proper crimping tool designed for ferrules to ensure a secure fit.
Safety Considerations
- Wire Preparation: Properly strip wire insulation without damaging the conductor. Excessively stripped or under-stripped wires can compromise the connection.
- Tight Connections: Ensure all connections are tight and secure. Loose connections can cause resistance, leading to overheating.
- Environmental Factors: Use connectors rated for the specific environment, such as waterproof connectors for outdoor applications.
- Load Capacity: Verify that the connectors are rated for the electrical load they will carry to prevent overheating and potential fire hazards.
Troubleshooting Common Issues
- Loose Connections: Inspect and tighten connections if you experience flickering lights or intermittent power.
- Corrosion: Check for signs of corrosion, especially in damp environments, and replace connectors as needed.
- Overheating: If connectors feel warm to the touch, this could indicate an overloaded circuit or a loose connection. Address immediately to prevent fire hazards.
- Wear and Tear: Over time, connectors may degrade. Regular inspection and maintenance can help identify issues before they become serious problems.
Future Trends in Wire Connectors
- Smart Connectors: Emerging technologies are integrating sensors into connectors to monitor the health of electrical connections in real-time, providing alerts for maintenance.
- Eco-Friendly Materials: Development of connectors using sustainable and recyclable materials is on the rise, reducing environmental impact.
- Enhanced Durability: Innovations in materials and design are leading to connectors that offer greater resistance to environmental factors and longer service life.
- Wireless Connectivity: Advances in wireless technology may reduce the need for physical connectors in some applications, promoting easier installation and maintenance.
Best Practices for Specific Applications
Residential Wiring
In residential settings, the choice of wire connectors is crucial for safety and efficiency. Here are some specific applications and best practices:
- Lighting Fixtures
- Connectors: Twist-on wire connectors or push-in connectors.
- Best Practice: Ensure connectors are rated for the voltage and current of the fixture. Check connections periodically for signs of wear or loosening.
- Electrical Outlets
- Connectors: Push-in wire connectors or screw-on terminal connectors.
- Best Practice: Use connectors that provide a secure and lasting connection. Avoid overloading outlets and ensure proper grounding.
- Appliances
- Connectors: Crimp connectors or twist-on wire connectors.
- Best Practice: Use connectors that can handle the high current draw of appliances. Verify that the wiring meets the appliance’s specifications.
Commercial Wiring
Commercial buildings often have more complex electrical systems. Proper connector usage is essential to handle higher loads and ensure safety.
- Office Lighting
- Connectors: Lever-nut connectors or push-in connectors.
- Best Practice: Utilize connectors that allow for easy reconfiguration of lighting layouts. Ensure all connections are properly rated for commercial use.
- HVAC Systems
- Connectors: Screw-on terminal connectors or crimp connectors.
- Best Practice: Ensure connectors can handle the higher currents and are resistant to vibration. Regularly inspect connections for wear and tear.
- Data Centers
- Connectors: IDC connectors for network cables and screw-on connectors for power supplies.
- Best Practice: Use high-quality connectors that minimize signal loss for data connections. Ensure power connectors are secure and can handle continuous operation.
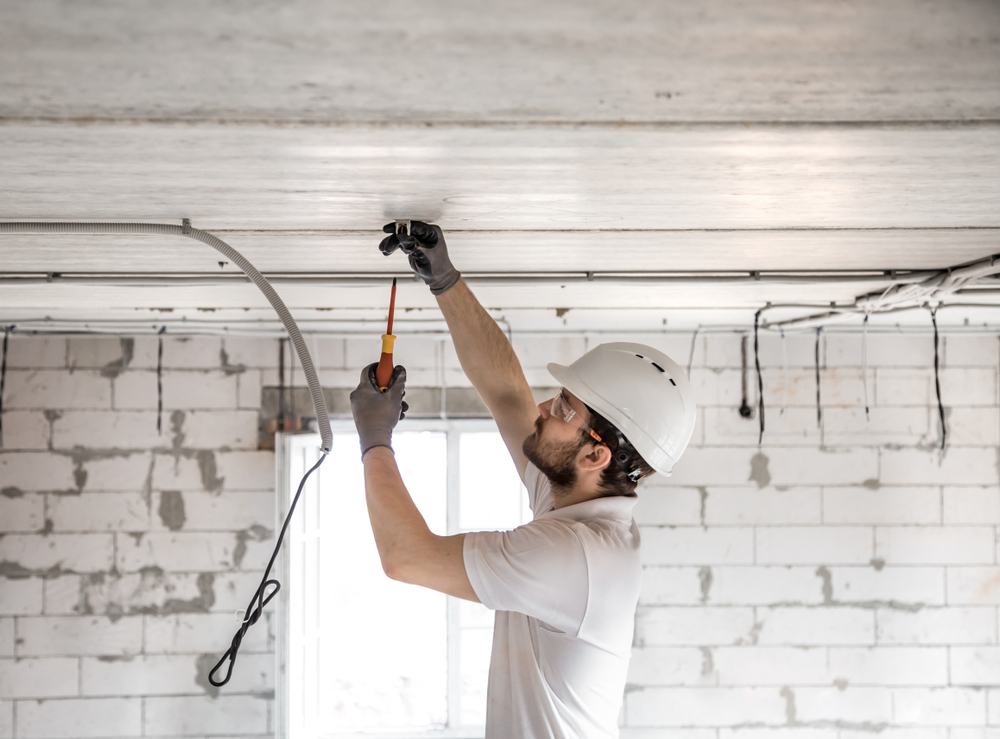
Industrial Wiring
In industrial environments, electrical systems are subject to harsh conditions and high loads, making the choice of wire connectors even more critical.
- Machinery
- Connectors: Heavy-duty crimp connectors or screw-on terminal connectors.
- Best Practice: Use connectors that can withstand high currents, mechanical stress, and environmental factors. Regular maintenance checks are essential.
- Control Panels
- Connectors: Lever-nut connectors or terminal blocks.
- Best Practice: Ensure all connections are secure and easily accessible for maintenance. Use color-coded connectors for better organization and safety.
- Outdoor Equipment
- Connectors: Waterproof twist-on wire connectors or heat shrink butt connectors.
- Best Practice: Choose connectors that are specifically designed for outdoor use, providing protection against moisture and temperature variations.
Regulatory Compliance
Compliance with electrical codes and standards is crucial to ensure the safety and legality of electrical installations. Here are some key points to consider:
- National Electrical Code (NEC)
- Relevance: The NEC provides guidelines for safe electrical installations in the United States.
- Best Practice: Always follow NEC requirements for wire connectors, including specifications for different applications and environments.
- Underwriters Laboratories (UL)
- Relevance: UL certification ensures that wire connectors meet safety and performance standards.
- Best Practice: Use UL-listed wire connectors to guarantee compliance with safety standards and reliability.
- International Electrotechnical Commission (IEC)
- Relevance: The IEC develops international standards for electrical technology.
- Best Practice: For global applications, ensure wire connectors meet IEC standards for consistency and safety.